January 28 and February 1, 2003 meeting notes
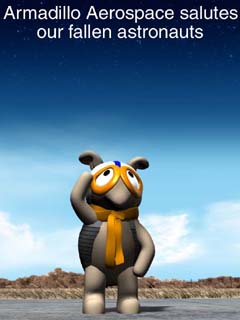
Small Vehicle Work
We did all the body wiring this week over 100 CPC crimp
connections.
http://media.armadilloaerospace.com/2003_02_01/cable.jpg
We are currently running lines for:
Four differentially throttled engine valves, with two lines
for the servo drive (switches polarity for direction) and three lines for the
pot feedback.
One master cutoff valve with the same wiring as the engine
valves.
One solenoid control with two lines for the CO2 drogue
ejection. We might consider adding
another of these for redundancy.
Two release latches with two lines each for the main chute
release. This is redundant.
A shielded cable for the tail camera.
We still have several free lines for future expansion. We will probably also be adding a pressure
transducer plumbed into the CO2 system so we can know for sure the drogue ejection
system is ready.
I could have reduced the total number of lines by making all
of the valve pots share the same +5V / ground signal, and the recovery
actuators could have shared grounds, but I decided it was easier to just run
separate wires. I dont have a firm opinion
on this call yet.
Having all this wiring does make me consider possibly moving
the electronics to an insulated box at the base of the vehicle, which could
eliminate all the cabling on this vehicle, but for the manned vehicles we would
have to run a bunch of lines back up for pilot control and display, so it would
probably just balance out there.
Big Vehicle Work
The vendor that we had expected to do the carbon fiber
filament winding on our big tank has backed out, and a couple more inquiries
hasnt turned anything up yet. Does
anyone know a composite shop that can wind a 63 x 144 pressure vessel (we can
provide the liner)?
Our stand-in fiberglass tank will be here in a couple
weeks. It will have the same mass we
are targeting the carbon tank for, but half the volume (shorter). We will be able to do all the flights
possible without a launch license with that tank, so we dont really need the
carbon tank for quite a while yet, but I wouldnt mind having it sitting in a
corner for when we are ready to use it.
The hatch reinforcement and sealing lip will be done next
week. This is necessary before we do a
crush cone drop test, otherwise it would likely buckle where the hole in the
cabin is. We have shrunk the hatch a
little bit, to a corner-rounded 24 x 30.
The extra reinforcement weight is proportional to the hatch size, and we
also want the hatch to be able to hinge down onto the tank end, which it cant
do if it is much taller.
The first full size crush cone (>7 tall!) will be done
next week. We are going to test this
before ordering any quantity. One point
worth noting is that we had originally asked for full seam welds inside and
out, with the outer surface ground smooth.
We later realized that having a fat weld on the outside really doesnt
hurt us much, because we will have the entire vehicle sprayed with thermal
insulation for the fast flights.
Dropping the inner seam weld and grinding saves a good chunk of
fabrication cost.
We debated doing a cabin pressurization test with the
boilerplate tank end, but we decided that cutting it out after we have sealed
it all up with RTV would be a pain, so we will just wait until we bond the
cabin to a real tank for the test.
Matt made an updated rendering of our current X-Prize vehicle
design, and to give it a really good sense of scale, he composited it into a
real photo of us working at the launch attempt in Oklahoma:
http://media.armadilloaerospace.com/2003_02_01/composite.jpg
One change I am currently thinking about is arranging for
the launch stand to grab the engine pods somehow, instead of requiring its own
set of hardpoints on the tank bottom.
Flow Sensor
We tested our S-Mass coriollis mass flow sensor on
Saturday. We are starting to use some
really large plumbing for this, with 2 flanges, fittings, and pipe / hose
throughout. The sensor reads up to 25
kg/s mass flow, which equates to a monoprop enging of nearly 7000lbf thrust. The response rate seems good, so this will
allow real-time Isp measurement during engine runs.
http://media.armadilloaerospace.com/2003_02_01/flowTest.jpg
The sensor is very picky about not having any trapped gas. We had to fiddle with it quite a bit to get it
working, and we arent yet completely sure of the right procedure to guarantee
that we can start a test run properly. It
wouldnt be a problem if we loaded the tank with vacuum, but the fiberglass
tank cant handle that.
For testing, we had an ugly chain of reducing fittings to go
from a 2 NPT to a 1 NPT to a ½ NPT to a manual ball valve. The flow was obviously very turbulent on
exit, but it was still a little surprising that with 250 psi behind it, only 5
kg/s of water would flow through a ½ ball valve under those conditions. There is really something to be said for
flanged connections over threaded connections, and we will probably have to
start paying more attention to smooth plumbing flow as we try and get more
performance.
We galled a 5/8 stainless bolt in one of the flanges, and
had to cut it off. I hate using anti-seize
on fasteners near something that may have peroxide sitting in it for moderate
amounts of time, because it always makes a mess that seems to get everywhere,
but stainless galls so easily that you really do need to.