More methane engine development, WSTF tests, high-pressure Mod work, and more...

May 5, 2009 notes by Phil Eaton:
List of Accomplishments since
the last update:
Methane engine Finalized and
coated internally by Ncoat Inc.
Methane engine Tested for NASA
with the J2-X Pyro Ignition Module.
Coaxial Swirl Injector
development.
V-Cut Ball valve results.
Self Pressurization issues.
New Coaxial Swirl Injector flies
Mod with Self Pressurized Propellants.
Rocket Tug Of War.
Linear Actuator issues fixed.
Methane Engine Run in WSTF
Altitude Chamber
Mod XL rebuilt and ready for
another test.
Class 3 Waiver progress.
Preparation for Free Flights.
Since the last update, we have been
pressing hard on many fronts. In addition, John has been so busy with
his duties at id Software, that he has not had time to make the
normal update himself. Thus you are stuck with the storyteller rather
than the technical presentations you may be used to.
NASA Methane Engine Work:
After the Methane engine had the nozzle
replaced, shown in the last update, we sent it to nCoat for a new R&D
coating they had produced designated H1008. http://www.ncoat.com/
You will have to contact them directly to request the H1008 above as
it is not yet on their product listing.
This coating was much better than a
previous coating they had done for us, and the only place it appeared
to wear was right at the throat. The coating is good for temperatures
in excess of 4000 degrees F for an extended period of time under
normal conditions. Under supersonic conditions as seen in the throat
of an engine however, it stresses it to the limit if not slightly
beyond. It still hung in there for the 3 tests we did here, and the
tests we ran in the altitude chamber at White Sands Test Facility in
Las Cruces.
Minor discoloration, a slightly
“melted” look and one spot that flaked off the surface
was all that happened to it over 3 to 4 minutes of firing. The
remainder of the areas that were coated look as new as the day we
received it. It was especially helpful on the large bell nozzle in
the altitude chamber. It really helped cut down on the heat the
nozzle would see as the film cooling is getting really thin by the
time the bell has expanded it out.
That said, we managed to do a static
test of the coated methane engine in the morning with one baseline
run using a normal torch ignition sequence.
Video (WMV, 1.4MB):
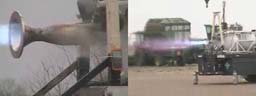
We did a second test using the J2X Pyro
igniter made by Pacific Scientific, which was the first ever ignition
of a LOX/Methane main engine with a pyro igniter.
Video (WMV, 1.5MB):
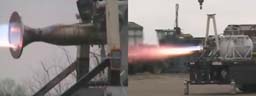
Photo courtesy JC Melcher (Click to enlarge):
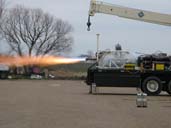
After a quick lunch break we had
installed the engine on the mod and ran the first ever flight of a
LOX/Methane powered vehicle with a Pyro igniter.
Photos courtesy JC Melcher (Click to
enlarge)
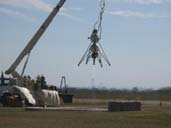
Video (WMV, 4MB):
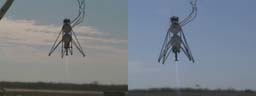
Overall it was one of those really
good days for Armadillo until later on in the afternoon; we
accidentally left a Li Ion battery pack on charge with the protection
circuits disabled. Yes, they really do explode and burst into flames.
The smoke is rather unpleasant as well, and filled the hanger rather
quickly! It was easily extinguished and did not cause any damage, but
it left us with a better sense of respect for the energy in those
batteries.
Coaxial Swirl Injector and Self
Pressurized work:
As soon as the work on the full density
engine for NASA was complete, we started working on a self
pressurized system in order to do away with helium pressurization,
and fill the tanks to their full capacity. This configuration doesn’t
have any performance gains for hovering or flights within the
atmosphere, but it certainly has some benefit if we can create a very
light weight, low pressure system as an upper stage and operate all
the way down to vacuum. It also may be an interesting direction to
pursue for longer and lower thrust runs on similar sized systems we
would normally use for pressure fed LOX/Alcohol.
We made an injector very similar to the
Like impinging full density injector with larger orifices, but there
was only just enough thrust to get the unit off the ground with the
propellants pressurized to 200PSI. This particular test was very
valuable however because we ended up short loading the LOX and ran
out of LOX before we ran out of LCH4. The transition was perfectly
smooth between liquid and gas phases. After reaching full throttle,
the vehicle gently descended with no ill effects. The same could not
be said when the LCH4 made its transition from liquid to gas. The
same effect of throttling up was occurring to a smaller degree, but
the fuel turning to gas was insufficient in the film cooling thus a
bright flash indicating burning stainless shortly followed. After
inspecting the engine, it had eroded at the throat only. Everything
else was intact.
We discovered that our results were
varying greatly depending on our hold time and discovered that the
tanks getting to pressure did not guarantee that the density had
gotten to the appropriate point. We moved back to testing on the sled
and installed thermocouples at the bottom of the tanks to monitor the
temperature. This was an excellent data point because the hold time
required to get the temperatures to the appropriate level were more
than double what we had been waiting previously. The initial runs
were autogenous blow down runs rather than a self pressurized run,
which was also confirmed in the pressure trace data. The tank
pressures clearly would fall off as soon as the run started.
At 200 PSI, the temperatures would
stabilize after about 45 minutes without touching the tanks. If we
took a broom to the tank and kept the Texas-humidity frost off of
them, the time would cut down to 20 minutes easily. It is amazing how
effective frost can be as an insulator. Finally we achieved a good
solid series of runs that had the capability of running at full
throttle and low throttle positions without burning the engine. We
had to increase the orifice sizes of the injector and the film
cooling to be much larger than calculations would indicate because
the lower density propellants would go to 2 phase flow in the
injector and restrict the flow capability coming through the
injector.
(Click to enlarge)
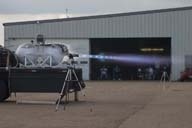
Matt purchased one of the new Casio
cameras that can do the high speed video in the last 2 months and has
had lots of opportunities to test it out. The video below is a really
good shot of start up and shut down of a self pressurized swirl
injector run at 600fps.
Video (WMV, 2MB):
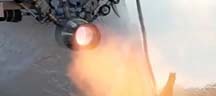
After the engine was verified on the
sled, we began testing on the vehicle again. It appears that we have
a good engine to proceed with now. It took us 4 tries to get the
swirler right for self pressurized hovering, but it appears to be
working now. It takes much longer to run on the mill than the old
designs, but we can get significantly better performance from it with
less L* than the Like Impinging injector.
The biggest problem with running self
pressurized as opposed to blow down is that the pressure in the tanks
remains constant within 5 to 10 PSI over the whole flight. This means
the engine has to throttle much deeper to offset for the difference
in weight from start to finish.
Our early attempts at V-Cut ball valves
indicated that there was a much higher restriction than anticipated
with self pressurized propellants, so we went back to 1” full
port ball valves. Unfortunately, the partial throttle positions seem
to be a little less precise than we would like, but it is still
working. We just have to change the minimum throttle position so that
we can land effectively without adding extra ballast weight.
Below is some 600fps video of the Mod
starting and shutting down on a hover using self Pressurized
propellants.
Video (WMV, 8.6MB):
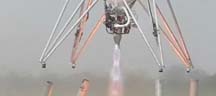
Now that the Engine is working
properly, we have begun doing some of the preliminary testing for
boost and return flights here at our home base under the new amateur
rules. We wanted to get a feel for how the vehicle would react to
sudden changes in wind speeds as it moved upward. The only thing we
could think of to induce a similar force was to attach a really long
cable to one of the legs and have someone pull on it during a hover.
Russ discovered that the rocket has a
significant amount of force to apply with gimbaling the engine, and
it amounted to him playing Tug Of War with the rocket in flight. The
gains were doubled from the first flight to the second flight so we
could see how the vehicle responded in attitude and position. This is
also the set of flights that we had problems with the linear
actuators. On both flights, one or both of the gimbals would go “off
scale” and freeze up.
Video (WMV, 9MB):
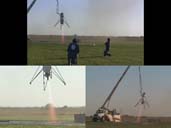
John made the call that we would not do
any further flights until we solved this problem, because we now have
not only the gimbals operated by these actuators, but the linked
throttle set up as well.
We spent a good deal of time dissecting
several actuators that had the problem on the vehicle. Oddly the
problem would not show up on the bench at first. I decided to
assemble a test unit that used a needle sweep to show the voltage
feedback rather than just read the voltage so we could test them
under the same conditions as the vehicle. That was still showing that
one of the actuators was good that was failing on the vehicle. We
then rigged up a ground strap that we could connect to the body of
the actuator, and Bingo, the failure showed up on the bench.
(Click to enlarge)
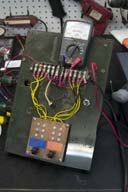
After pulling the bad units apart, it
was discovered that after using the units for a while, the ball screw
nut housing was rubbing on the wiring at the top of the resistor area
and when it got through the insulation on the wire, it would short to
the housing and cause the failure. The problem did not show up if the
housing was not grounded.
Russ and I looked at the units and
decided that if we turned the resistors around and made the wiring
for the feedback come out at the bottom there would not be anything
to hit it, and it should fix the problem. We built up one unit first
and verified that this worked extremely well. It also changed the
dynamic of the voltage so that if it did go off scale at the full
retract position, it was on the zero volt side, and the unit would
just stop driving. It would not present itself as a lock up failure
as it could still drive the other way when commanded. The other units
were modified to match and reinstalled on the vehicle.
We then did another Tug of War test the
same day, and this time we were able to vary the gains between the
Position hold and Attitude control. We ended up with a position hold
of 1 and an attitude control at 1.5 that seemed to work the best.
During the first flight you can see as
the gains are varied from one pull to the next. On the last pull,
Russ decided not to pull as hard, but kept steady pressure on it and
followed along with the rocket until it went farther than we wanted
so we shut it down.
On the second flight, we had the gains
dialed in to balance the attitude hold plus position hold parameters
without as many oscillations. Right at the end of the test, is where
the vehicle ran from self pressurized methane to gaseous methane
followed by a nice bright flash.
Video (WMV, 11MB):
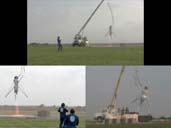
Linked Valves: (Click to enlarge)
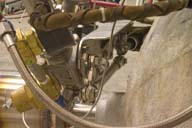
NASA White Sands Test Facility
(WSTF) testing
While we were running all of the Self
Pressurized testing, the NASA folks were installing the Full Density
Methane engine in their Altitude Chamber and preparing for the runs.
There were a few problems however.
Photos of engine alone mounted courtesy Jacob Collins (Click to enlarge)
Normally for an engine this large they
would run the Large Altitude Simulator System (LASS). This system is
basically 3 LOX Isopropyl Alcohol Rocket engines with a very large
steam injector system that creates enough volume and pressure steam
to pull the chamber down to 160,000 feet and hold it there when the
engine inside the chamber is running. The water is pumped by 4 very
large Diesel engines, and the alcohol is pumped by 3 smaller diesel
engines. Following is a nice photo sequence of the LASS Set up.
(Click to enlarge)
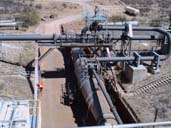
Unfortunately, they have had some
personnel turnover lately and the only person certified to run the
system had suffered a stroke the week before the test. We all hope
the best for him and a quick recovery!
This left the option of running the
system with the Small Altitude Simulator System (SASS). This unit
could only pull down to about 120,000 feet, but it could not hold it
there during the run. This was a desirable situation for us to have
though since we were running a dual bell nozzle. One of the things we
wanted to see was a sweep in the altitude to see if the nozzle would
jump from one bell to the other without a bad thrust vector from
gasses delaminating in a non symmetrical fashion. Normally, they
would hold this as a very undesirable condition but under the
circumstances, the whole NASA team was pulling out all the stops to
make this the best test they could provide. We were GO for SASS!
Following is some photos of the Control
room where all the magic happens. After seeing this, I was motivated
to upgrade John’s station from a card table to something a bit
nicer, but that will have to wait!
Photos courtesy Jacob Collins (Click to enlarge)
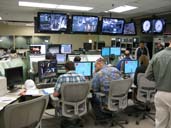
Everything was in place and they ran
the baseline 5 second runs at ambient pressures. We are ready for the
Dual Bell installation and Altitude runs. The first run is going to
use the pyro igniter, and the chamber will be set initially at
117,000 feet with a planned run time of 5 seconds.
The Fire sequence is initiated with a
“Fire Red”, and after the initial LOX dump, the engine
throttles up simultaneously with the torch ignition. There was a
bright flash that obscured mostly every camera in the chamber, and a
half second later, the video screens show a beautiful blue flame
fully expanded in the 26” nozzle!
(Click to enlarge)
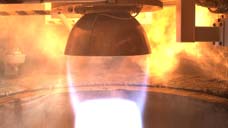
Unfortunately, the temperatures
elevated to a level higher than expected so the test was terminated
right at the 5 second mark with a “Fire White” call.
We shut down for the rest of the day to
evaluate the data. As it turns out, the 200 milliseconds between main
valve open and ignition provides a rather large supply of Methane and
LOX to dissipate. At ambient pressure it just burns away quickly
below the engine. At 110,000 feet however, the ambient pressure being
less than 1PSI causes the cryogenic material to expand much more
quickly. When it ignited in the altitude chamber, it caused a rather
large fireball that extended above the engine area up into the 2nd
story of the altitude chamber.
We reviewed the high speed data and
reworked the ignition sequence to do away with the LOX Pre-chill, and
just start with a 200Msec LOX lead. We would also be using the
Armadillo torch igniter rather than the pyro igniter this time. We
also compared the ignition sequence to the LOX/Methane run they did
last year with the old Lunar Lander RS-18 engine. It had slightly
more thrust, but was close enough to be comparable. That engine was
run using the LASS. The engine ran between 1 and 2 seconds long, and
showed a visible flash right at the start just as ours did, but
running the LASS as opposed to the SASS, the eductor was able to
pull all the remnants of propellant out the eductor rather than it
all dissipating into the chamber.
The sensors in the chamber recorded
temperatures in excess of 250 degrees F within the 5 seconds of the
run. It was not clear if this was from the extraneous burning, or if
it was the accumulation of heat in the altitude chamber due to the
SASS not being able to pull all of the gasses out of the chamber. The
Thermal sensors were shielded to make sure that they were not picking
up radiated energy, and everything was reset for another try.
The plan was to run the engine for a
full 20 seconds this time and start at the highest altitude they
could, 120,000 feet, with the SASS.
The engine is fired, and the flash was
still present although much more subdued. Jen Allred, the person
taking the lead on our project for the WSTF facility, is staring at
the temperature graphs of the chamber hoping that the temps stay
below any level that they think might cause damage to the test cell.
The High Def Video returns a beautiful flame coming from the monster
bell once again, but this time, you can visibly see the altitude
change affecting the shape of the plume. Jen held on for nearly the
full 20 seconds, calling “Fire White” only when the
temperatures spiked above 600 degrees F!
Following is a gorgeous video of the
run from the main High Def Camera. You might have to turn your volume
up a bit to get the full effect…
Video (WMV, 3.4MB):
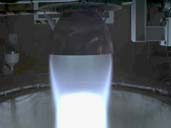
If turning the volume up doesn’t
work, play some other rocket video at the same time. It just doesn’t
sound right like that!
Mod XL Work
Between Swirl Injector iterations, we
managed to put in some time on the Mod XL, AKA the Pressurized
Module. Well, at least James got a chance to put in a bunch of work.
It is completely recovered from its cartwheel event, and nearly ready
to fly. We need to do a few water tests before we load it back up and
take it to the pad for another go, and we still have to fabricate 2
additional attach points for tethers so we have it hanging on 4
points around the tank instead of 2. And yes, we will be using Grade
8, 7/16” bolts all the way around.
(Click to enlarge)
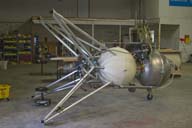
Very soon we hope to be able to fly our
final milestone flight from NASA with the Methane mod using the Self
Pressurized system in a full free flight. Right after that, we will
be ready to start doing boosted hop style testing. The Mod XL is
right behind the Methane Mod on the priority list. As soon as we get
a few boosted hop flights out of the way, we will start getting LLC
level 2 parameters nailed down on the Mod XL. We will not do any
boosted hop flights with the Mod XL until we can successfully close
the chapter on the Level 2 LLC prize.
FAA Waiver Update
One of the reasons the update is so
late in coming is because we have been waiting for a recommendation
from AST to the local FAA office on the Class 3 Authorization for
flight at the Caddo Mills Airport. We thought that the process would
be a mere formality, and hoped that the full 45 days would not be
required. Since this was one of the first class 3 waivers they had to
process however, we had to do a bit more work than expected, and they
had to figure out exactly how to make the process work on their end.
As it turns out, we are getting mighty close to the 45 days from the
time we first turned in the application, but I have already received
confirmation that they will have their recommendation ready by the
end of next week at the latest.
The process of getting the waiver
approved has actually been a rather lengthy task. It started in mid
to late January, and proceeded through February by having conference
calls with the airspace managers and the local specialists that write
the waivers. We finally set up a time for all of the FAA Managers and
Airspace Managers to come to the shop for a presentation and demo
flight operation. There was clearly a misconception of exactly what
Armadillo Aerospace does in comparison to other high power rockets.
While Craig McFadden and company looked
over John’s shoulder, the procedure and flight went extremely
well. Of course our Control console is nowhere near as impressive as
the one at WSTF!
(Click to enlarge)
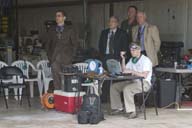
We followed that up with a basic
presentation of our history, how we compare to other rockets, and
what we wanted to do in the future. They also brought some extremely
valuable data that showed the flight rates through our area and at
what approximate times. It just so happens that there are 2 major
departure corridors just to the North and South of our location. In
spite of this, the general feeling of everyone present was that we
had enough control over our vehicles that we would be able to fly on
cue within windows they could give us, and certainly prevent any
breech into airspace that they needed us to stay clear of.
For all of you following and
contributing to the recent threads on ARocket; all of this means that
the next update should hold some really cool video of an Armadillo
Rocket flying free on the Texas horizon, “like
God and Robert Heinlein meant them to!”
By the way, Russ Blink might have something to say about the first man to ever fly on a purely rocket powered VTVL vehicle on the Earth…
|