May 7 and 11, 2002 Meeting Notes
In attendance:
John Carmack
Phil Eaton
Russ Blink
Neil Milburn
Joseph LaGrave (Saturday)
We expected to do more high speed rotor testing, but the new
tubing didnt make it on time. We did
get another large solenoid, and Russ has made a new sensor circuit, so we are
basically ready to go as soon as we can re-plumb the rotor. We also changed the tank mounting on the
trailer so we can use it for both the horizontal test stand and the vertical
test stand without having to move it.
Big engine
The two 5.5 ID stainless engines from DynaTurn made it in,
and they turned out great. I originally
intended to make a copper sheet gasket for it, but we went ahead and tried it
without a gasket, and it seemed to seal fine just on its 20 bolts.
It turns out that we got perfect engine performance with only
60 silver screens in this engine, while we needed 70 in the 1 ID engines, so
there seems to be some beneficial scaling factors as work.
On Tuesday, we made several very smooth test firings, but
the performance was off a bit from what we expected. The throat was fabricated fairly sharp coming from the 45 degree
converging angle to the 15 degree diverging angle, so Russ took it home and
rounded it off a bit. This did increase
the throat area a bit, but our tests on Saturday showed both more thrust, and
higher Isp. In fact, the 122 Isp we
measured is the highest we have seen from any of our engines. We also had a kinked hose on Tuesday, so we
cant for certain attribute the large performance boost to the smoothed throat,
but it is probably a good bet.
www.armadilloaerospace.com/may11_02/fivefive.xls
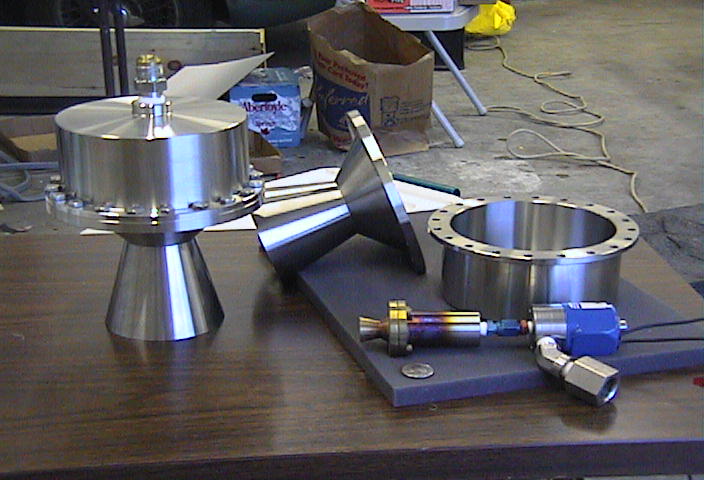
Chain Hoist Balance Test
We finally got around to hanging up Russs chain hoist, se
we can lift the vehicles from a single point to properly balance them.
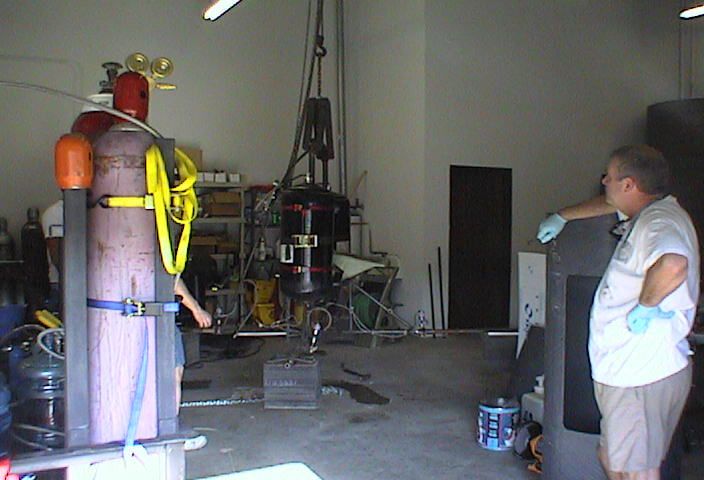
Attitude engine plate
The 2 diameter vehicle will have offset side firing
engines, unlike all of our vehicles so far, which have had canted down firing
engines. We are using 1.25 tubing
clamps to mount the engines, and we were just barely able to rigidly connect
pairs of solenoids together with a T fitting, so we will only need to run two
hard lines on the bulkhead. We had to
remove the outer solenoid casings and grind a little off the retaining bolt,
but it was worth it for the compact plumbing arrangement.
The mounting bulkhead is just 3/8 playwood, but we sealed
it with epoxy to make it peroxide safe. The picture just shows them laid up on the press board that
stiffened the filament wound tubing for shipping, not our real bulkhead.
.
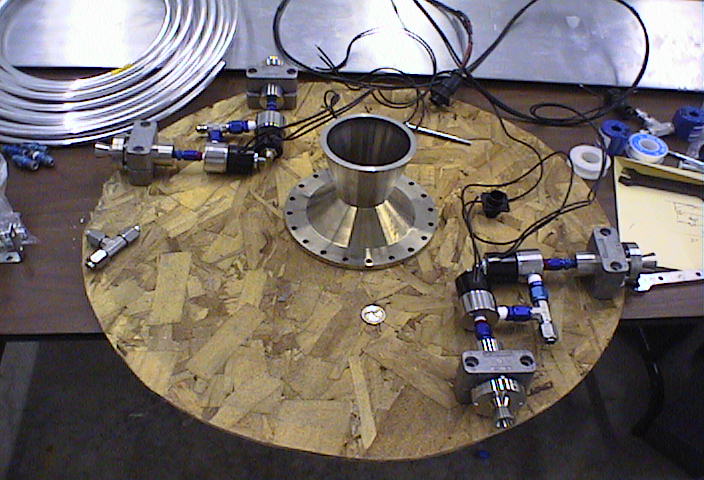
Cabin Hatch
We fitted internal retaining slides to the 2 tube for our
lexan hatch. We had been planning on
making the hatch slide into a pocket on the bottom, and have a dog on the top,
but it turned out to be easy to just make sides on the top and bottom, and
slide the lexan to the side for getting in and out. We are just going to put two bolts through the lexan on the side,
with a strap between them on both the inside and outside. The bolts will also serve as slide
stops. This is not intended to be a
pressure tight cabin, just an aerodynamic fairing.
We should have left it alone after we had it all set up, but
we tried to heat form the lexan sheet so it wasnt sprung so tightly into the
tube. A heat gun didnt get it hot
enough to soften sufficiently, so we went after it with a torch for a
while. We got it curved a bit, but when
we tried to straighten out the edges a bit, we wound up making bit of a mess of
it. We are probably going to have the
plastics company that made our test stand shield curve another piece for us.
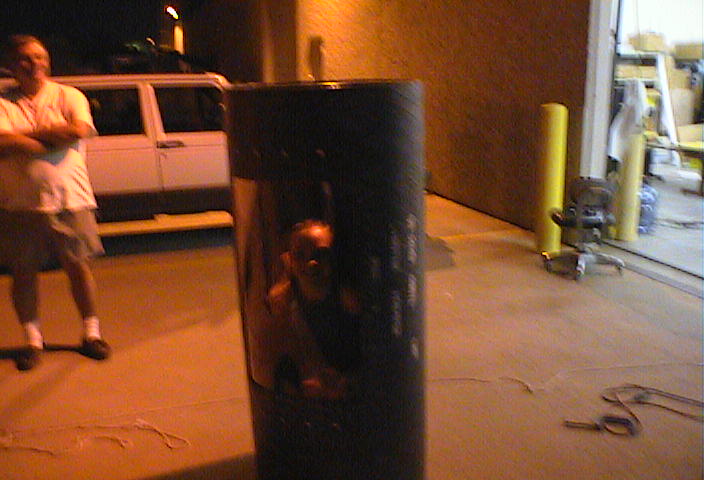
Upcoming Work
Full speed rotor testing
Replace
tubing
Water flow
the large solenoid for comparison
Test new
tach sensor
Attitude bulkhead testing
Finish
mounting and tube bending
Mount in
tube
Mount top
bulkhead with eye bolt in place of rotor hub
Make an
eight conductor CPC extension cable
Have Joseph
bring his Bobcat to suspend it outside
Big lander flights
Replace Ethernet
board in flight computer
Finish new
software architecture
Make new
mounting bracket for main engine
Precession attitude control tests
Add rotor
RPM control to flight computer
Get more
chain for tying down all four corners of the lander at the pad
Bore out one of the 1 engine nozzles from 0.33 to 0.45 to
see if we can use a larger throat to pack ratio
2 ID engines will be in next week
Regeneratively cooled chamber with
integral fuel injector
Tap
¼ NPT into the bottom of the spare NOS tank so we can run higher pressure
kerosene
Radiatiively cooled chamber
Fuel injector ring
Clamp ring for
non-bolted chamber
Fabricate
brass mockup and test with flood cooling
Get TZM to DynaTurn
Platinum
plate at Dallas Precious Metals
12 ID engine
Pay for
silver screens
Find
someone to roll the nozzle
Weld
everything together and cleanup
Fabricate
reinforced perforated metal retaining plate
High speed flight
Fabricate a sheet metal nose cone /
rotor spinner
Test new
parachute rocket system